T-08: Caseback
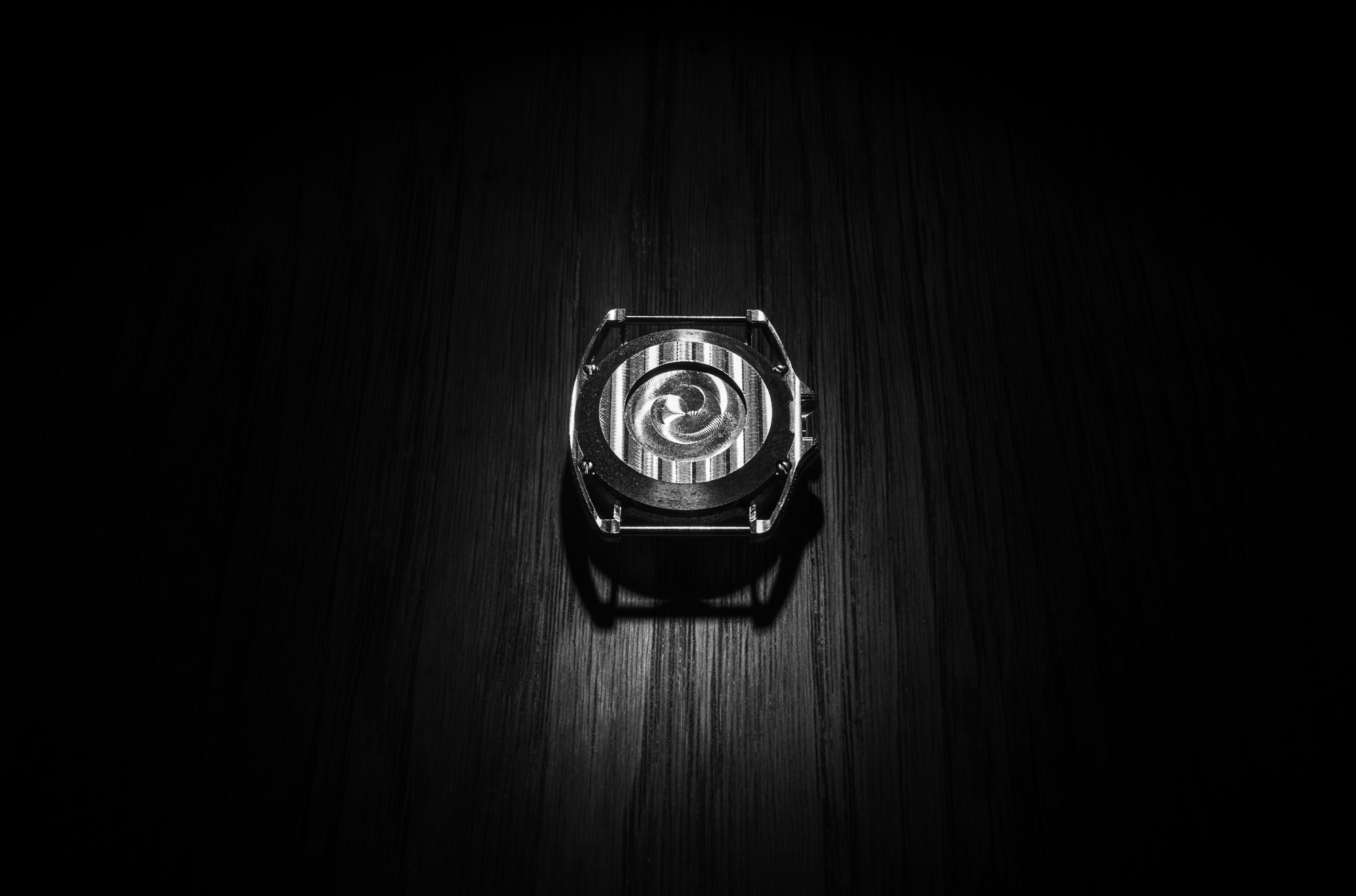
Wear and maintenance in space
The harsh environment of space, with its extreme temperatures, vacuum, and radiation exposure, significantly affects the performance and longevity of any type of hardware. In this unforgiving setting, materials behave differently than they would on Earth. The wear behavior of components is also significantly influenced by factors such as thermal expansion, brittleness due to low temperatures, and the absence of gravity. This demands a thoughtful approach to material selection and design to ensure optimal performance, longevity and maintainability.
When it comes to maintenance, the absence of gravity creates an environment where simple tasks like placing a screw or fastening components can become incredibly challenging. Without the familiar force of gravity to provide stability, astronauts must rely on careful coordination and specialized tools. The vacuum environment poses another hurdle, as it can accelerate the degradation of materials. Furthermore, the constant exposure to radiation in space adds complexity, degrading electronic components and impacting their reliability.
The difficulty of maintenance and repair work is further compounded by the fact that there are limited resources accessible in space. Unlike on Earth, where supplies can be readily replenished, space missions face the constraints of resupply missions, which are costly and infrequent. As a result, astronauts must carefully manage their available resources and ensure they have the necessary tools and spare parts for maintenance tasks.
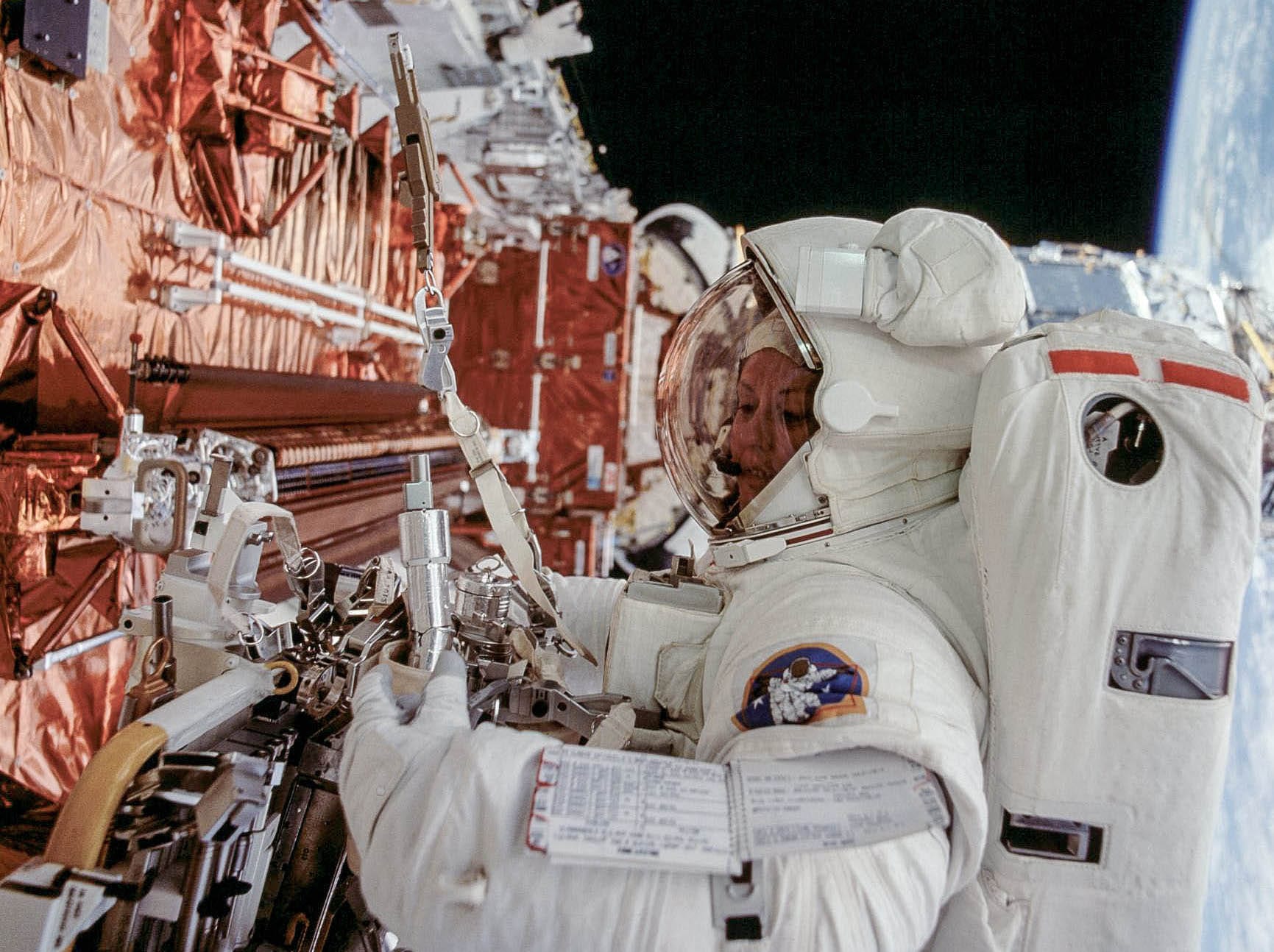
Building products for space: best practices
Building products for space exploration requires adherence to stringent requirements and best practices to ensure reliability and maintainability. Key considerations include avoiding single points of failure, promoting standardization, and prioritizing simplicity.
By incorporating redundant systems and standardized components, engineers can maximize the utilization of limited resources. Redundancy ensures that failures in one system can be compensated for by backup systems, mitigating the risk of mission failure. Standardization simplifies the process of maintenance and repair by enabling the interchangeability of parts, allowing astronauts to use a single set of tools and procedures across different systems.
One example for implementing these principles is found in the part numbering system established by NASA, which sets a standard for the identification and categorization of components used in space missions. By following NASA's part numbering standards, engineers ensure that critical components can be easily identified, sourced, and replaced when necessary. This system simplifies maintenance procedures and reduces the risk of errors or delays during repair operations.
Another important guiding principle is simplicity. While complexity is sometimes valued in certain products like traditional mechanical watches, space hardware prioritizes simple and effective designs to reduce failure points and increase reliability. Simplicity improves ease of maintenance and overall operational efficiency in the demanding context of space exploration.
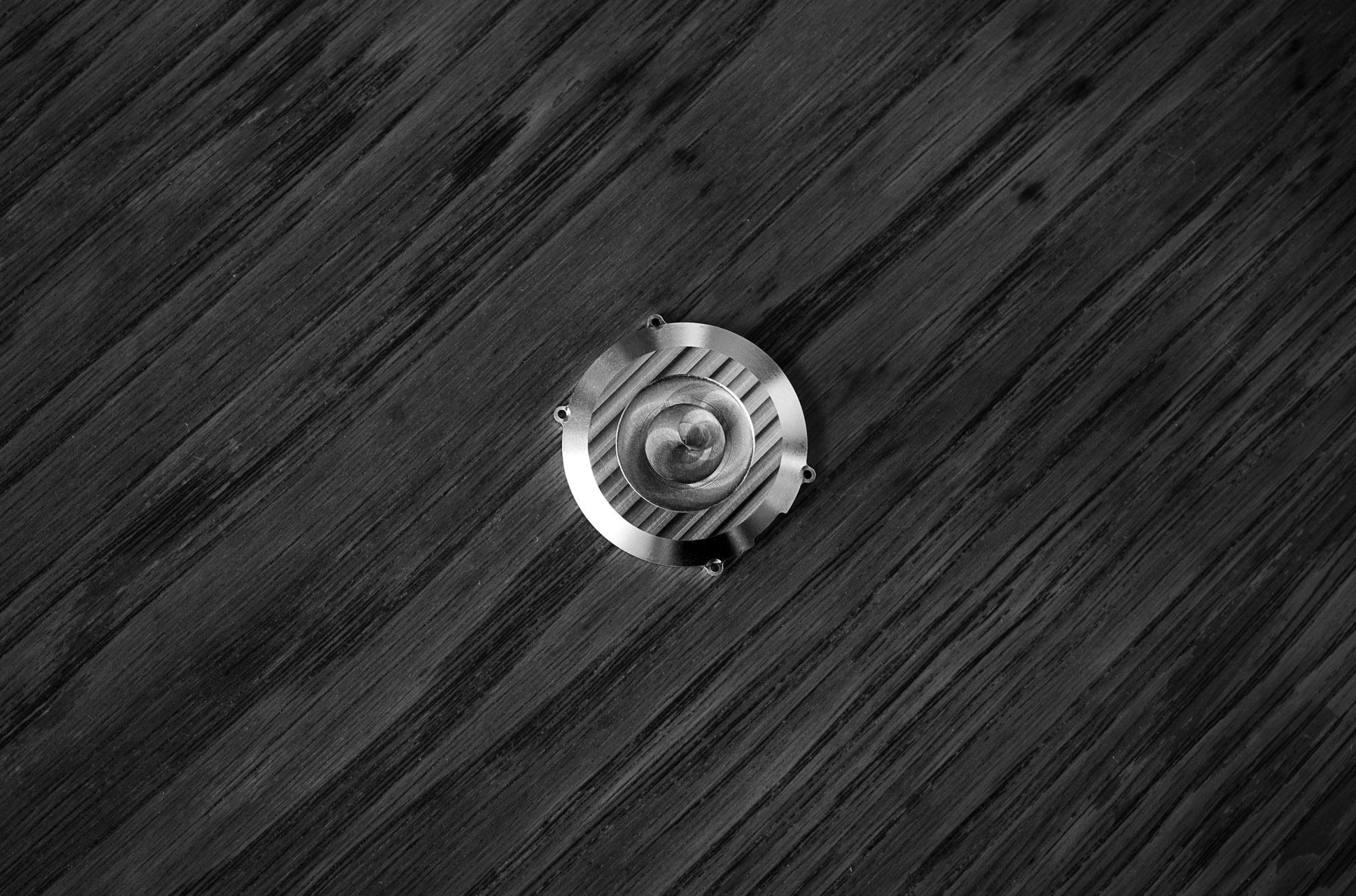
Monolith caseback
A simple yet highly effective construction is at the core of Monolith’s design philosophy. The Monolith caseback is a great demonstration of a seemingly simple component intentionally designed and executed to withstand the challenges posed by the harshness of space.
The caseback is constructed from 6061 aluminum alloy characterized by its exceptional strength-to-weight ratio, ensuring durability while minimizing the weight of the watch. Titanium screws are used to secure the caseback due to their extremely low thermal expansion coefficient, ensuring a consistent compression between parts even in extreme temperature gradients. Titanium is also well known for its excellent corrosion resistance and ability to withstand extreme conditions, making it an ideal choice for space exploration.
The gaskets used in Monolith's caseback will be a custom silicone elastomer based on Parker Seal’s S0383-70 approved for docking and airlock systems on the International Space Station. Thanks to their exceptional temperature stability, these gaskets maintain a reliable seal, even in the face of extreme temperature fluctuations, preventing the ingress of dust, moisture, and other contaminants.
To enhance the watch's durability further, we are currently exploring various types of coating. One path we are exploring is a Type III hard anodize, which refers to an electrochemical process that creates an extremely hard, abrasion resistant oxide layer on the surface of aluminum. Another path is a DLC (Diamond-Like Carbon) coating, which is an extremely durable layer of carbon with a hardness comparable to that of diamond. The DLC coating not only significantly reduces the likelihood of scratches but also imparts a sleek black color to the watch. However, in the event that scratches do occur, they become more noticeable due to the contrasting black DLC coating on the underlying aluminum.
Following NASA's established standards, we have implemented a comprehensive part numbering system to uniquely identify the complete watch and its various sub-components. To meet the international standards set for the aerospace industry, we have partnered with manufacturers that are ISO 9001 and EN9100 certified.
Monolith's caseback embraces a simplistic architecture, aerospace-grade materials, and a rugged design that minimizes potential points of failure. Currently, we are at the 14th design iteration and we are always open to feedback and insights - both technical and visual. Internally, we are still discussing between a clear hard anodize caseback or a gunmetal DLC coating, which is primarily an aesthetic consideration given that both paths will meet the technical requirements. If you would like to share your thoughts feel free to shoot us an email or message us on Instagram.
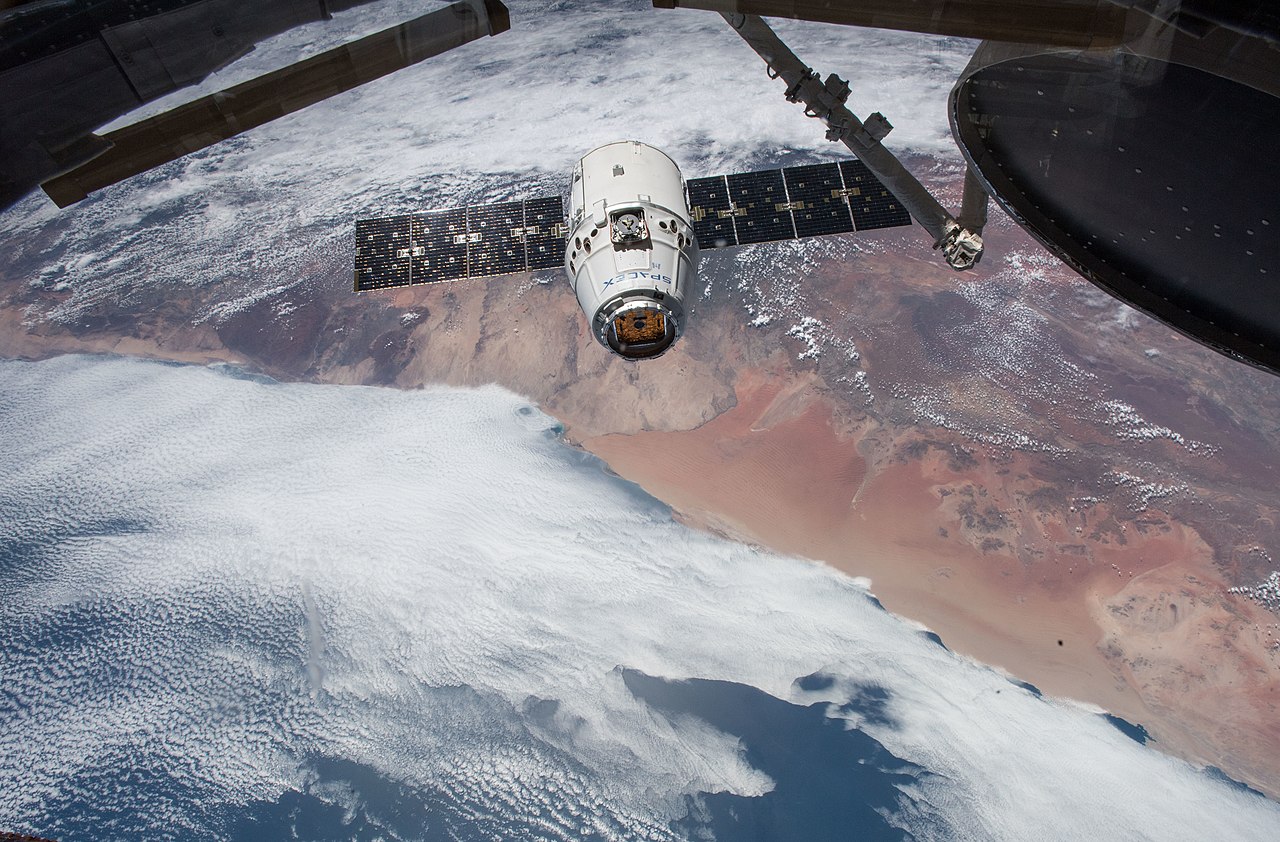
.jpg)
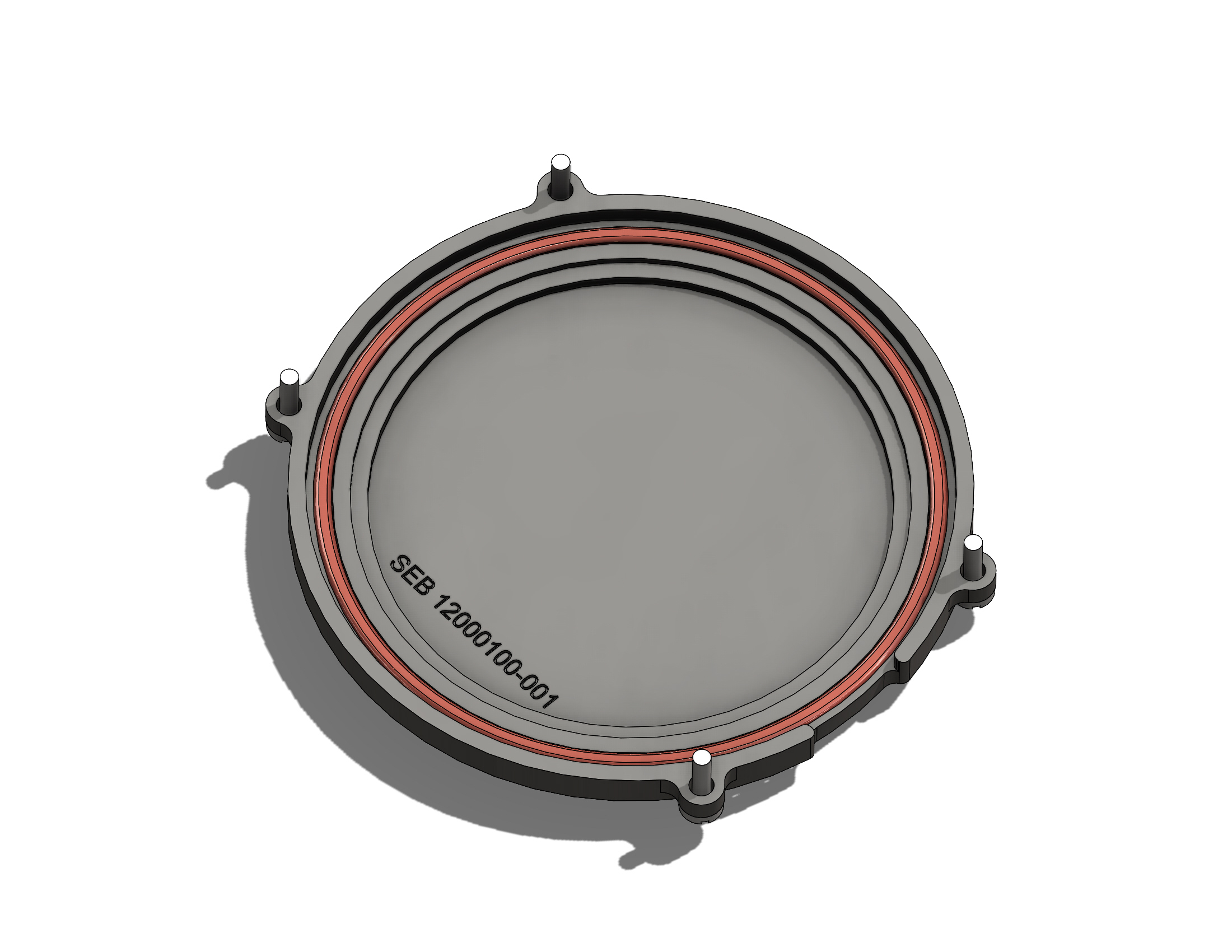
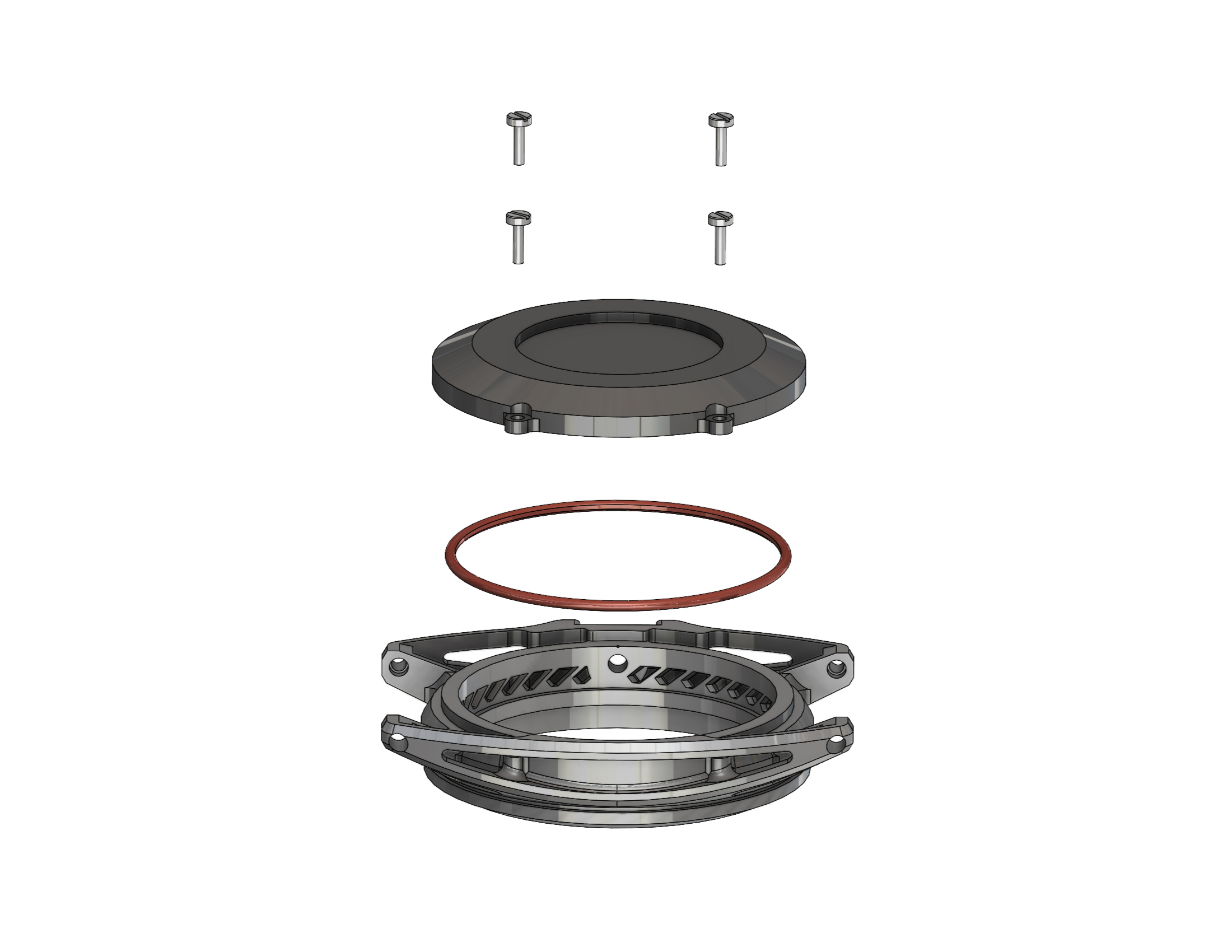
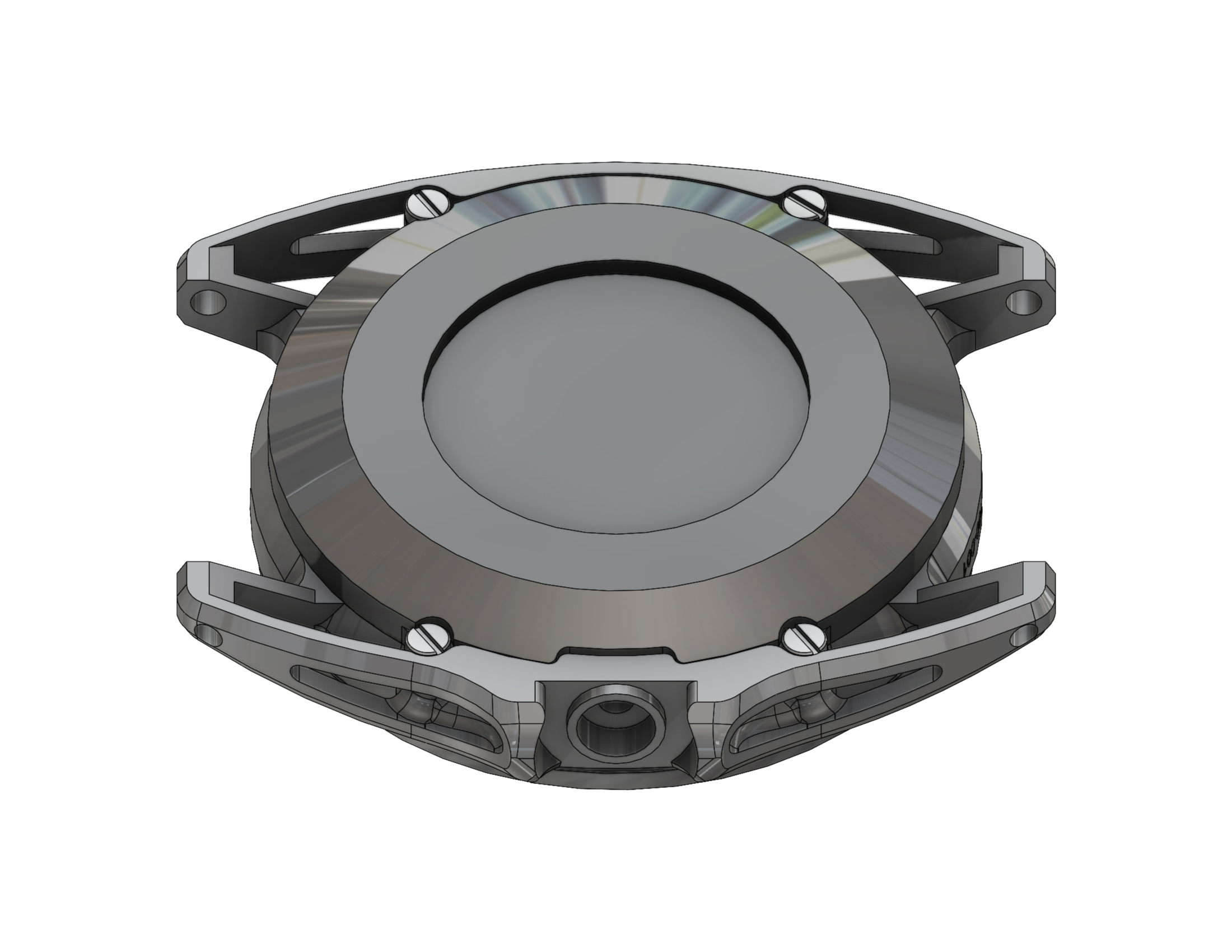