Own the technologies of tomorrow, in a product made today.
Window to the Future
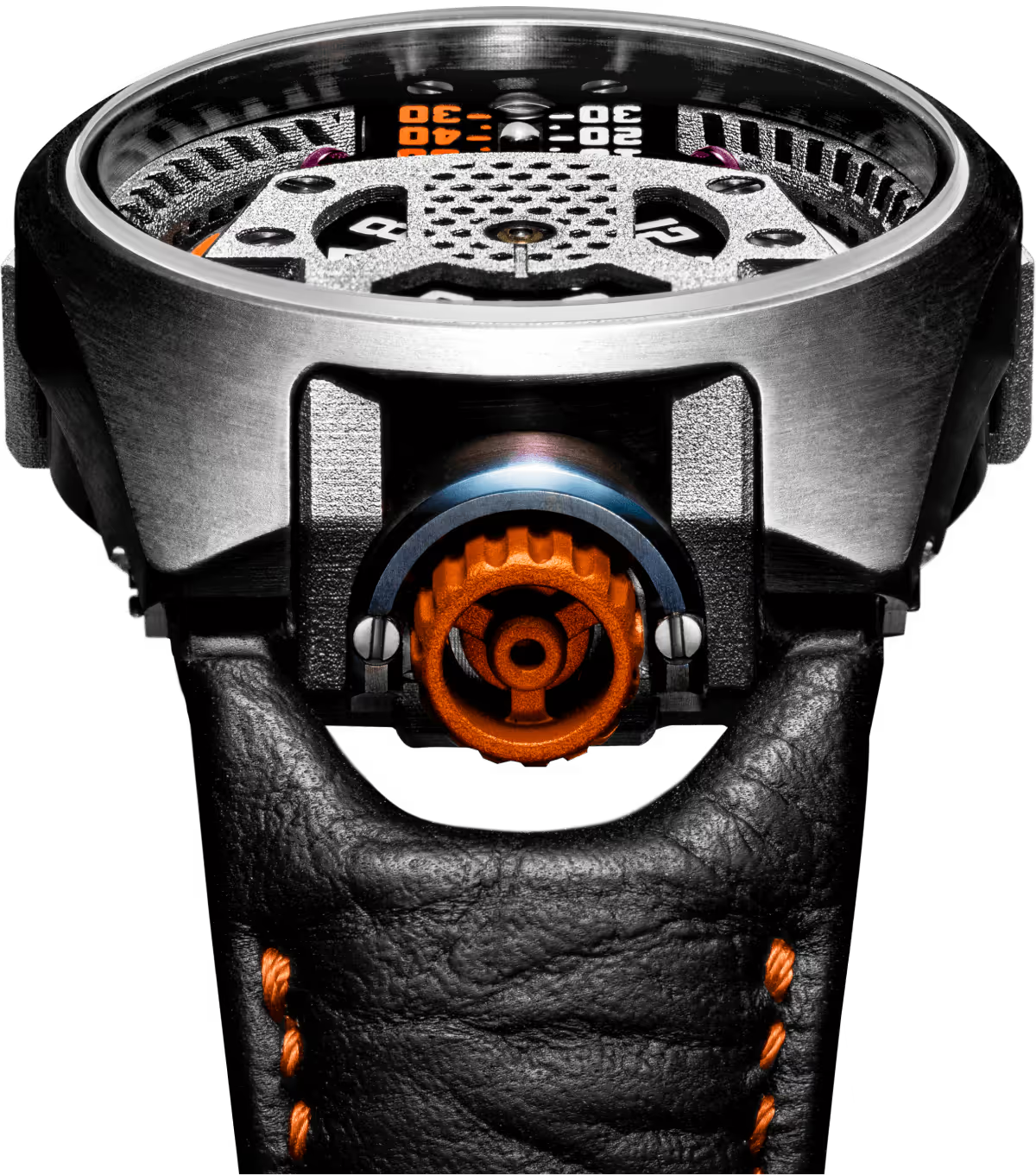
We use emerging technologies and ideas to build products for the next chapter of space exploration.
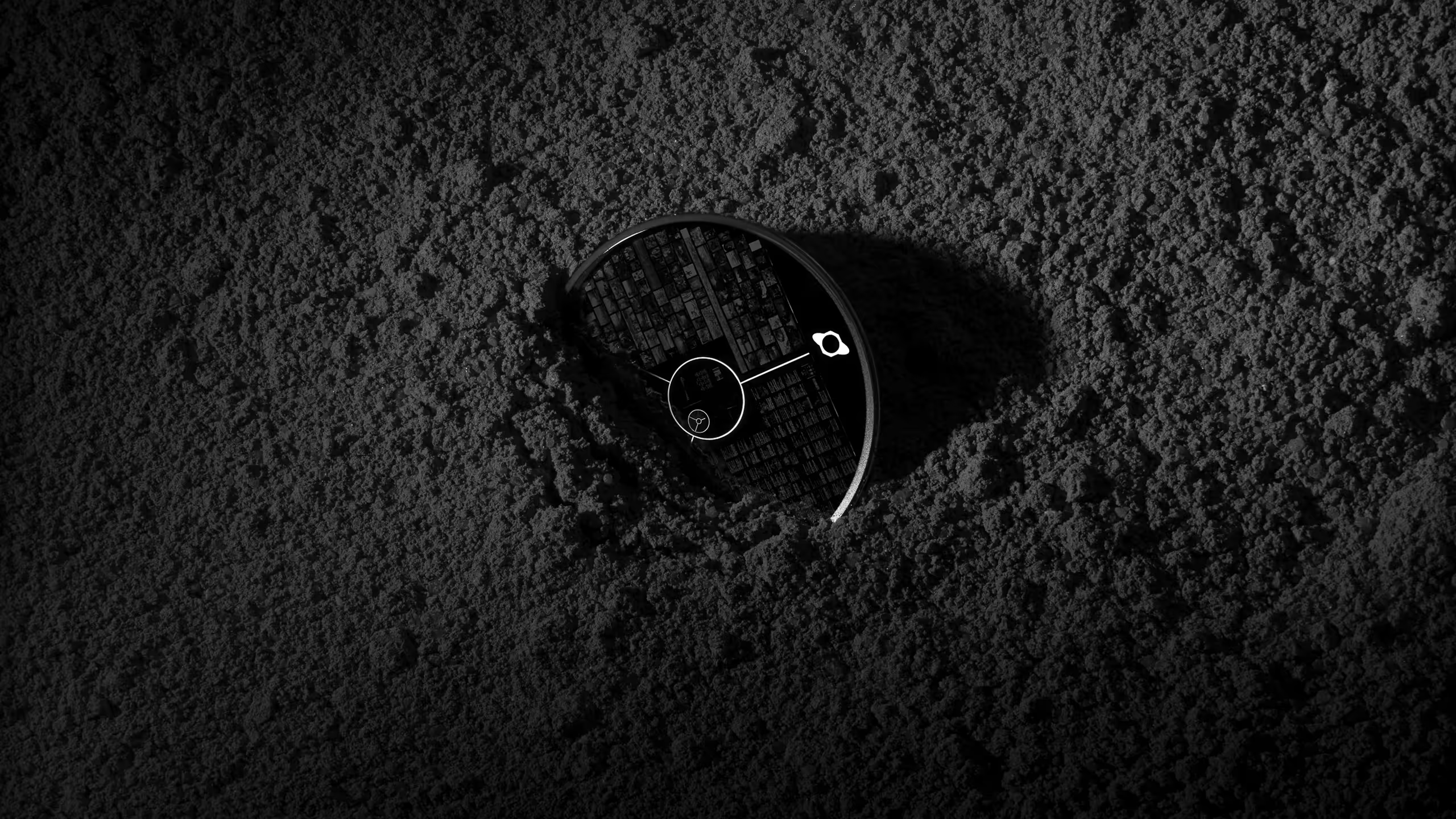
Barrelhand is a platform for innovation. We invite scientists, engineers, artists, and space enthusiasts to collaborate with us in creating products for the next frontier.
Learn more