T-10: 3D Printed Chassis
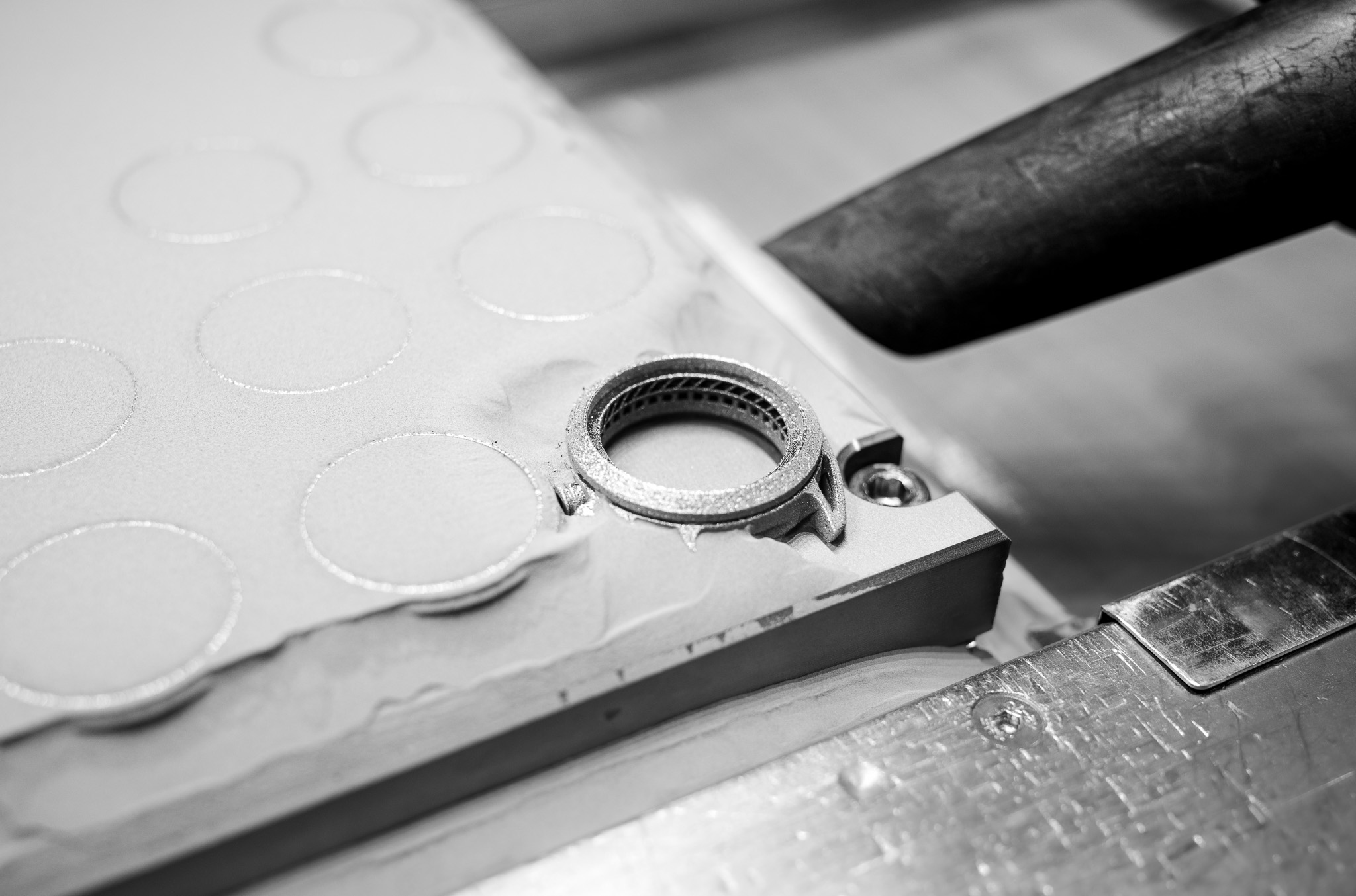
Getting to space (and staying in space)
Space is hard. Its harsh conditions present numerous obstacles that can make the difference between success and failure incredibly slim. Once we leave Earth’s atmosphere, we are confronted with a hostile environment and a variety of challenges such as extreme temperatures, microgravity, vacuum, and high levels of radiation — all of which require sophisticated technologies to allow any kind of exploration. However, before we’re even in a position to worry about space, we first need to be able to leave Earth’s surface, get to space, and stay there.
While space begins, depending on the definition, at a mere 62 miles above Earth's surface (known as Kármán line), there is a major difference between reaching “space” and reaching “orbit”. In order to not fall straight back to Earth’s surface, a spacecraft not only has to fly up, but achieve its escape velocity — the minimum speed required by an object to escape the gravitational pull of the primary object. In the case of Earth, a spacecraft has to travel at nearly 25,000 miles per hour in order to not fall back to the surface.
The energy required to achieve escape velocity on Earth is significant. In fact, around 90% of the mass of a rocket constitutes propellant, which is burned within minutes of the launch. To put it differently, every time you add ~1kg of cargo, the rocket needs an additional 10 kg of fuel.
This also explains why rockets throughout human history could only be used once and were completely destroyed after delivering their payload to orbit. Every component of the rockets was designed to reach orbit and nothing was added for a safe return back to the surface. Imagine booking a plane ticket from the US to Germany and upon arrival, you throw away the plane. Those flight tickets would be extremely expensive. This has been the reality of spaceflight — until recently.
Just a few years ago, SpaceX became the first manufacturer to achieve the holy grail of rocketry: launch systems that are able to deliver payloads to orbit and subsequently return back to Earth in one, reusable piece.
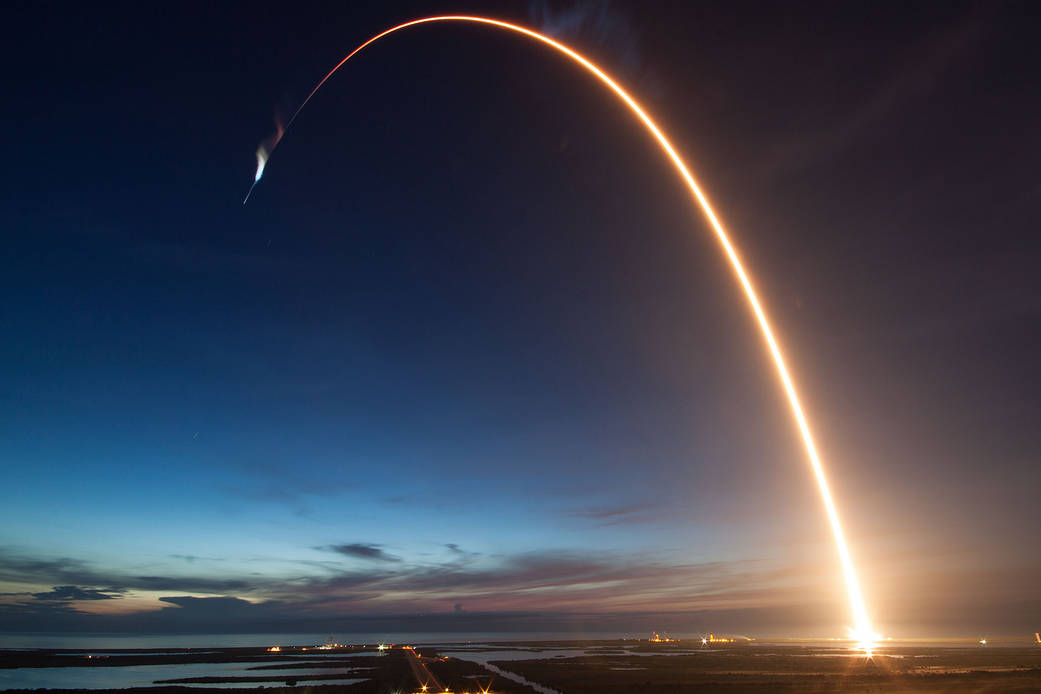
Contributions of additive manufacturing (3D printing)
3D printing has played a significant role in the development of reusable rockets. At the same time, the technology still holds vast untapped potential for other applications.
Traditional manufacturing typically works by means of subtraction: you start with a block of material and you remove parts of that material until you achieve the desired shape. In contrast, 3D printing — also known as additive manufacturing — produces objects by adding layers of material until the desired shape is achieved.
3D printing is an umbrella term encompassing an array of technologies capable of processing various types of materials. What they all have in common is that the conception of an object starts in the realm of software and requires fundamentally different thinking than preparing designs for conventional methods of fabrication. Anything that we seek to create in the physical world is limited to some extent by the available methods of fabrication. 3D printing removes many of the traditional limitations and allows us to fabricate designs that can be significantly more optimized toward their designated purpose.
Take the example of rocket engines, which are extremely complex systems, constructed out of thousands of individual components. There is now a new generation of space technology companies, such as SpaceX and Relativity Space, that are able to leverage 3D printing to reduce the total number of parts in those engines by a factor of 100. This translates into vastly more efficient engines with a better thrust-to-weight ratio, higher reliability, and massive improvements in their manufacturability at scale. 3D printing has also enabled significantly faster part delivery and higher flexibility due to simpler supply chains.
At the same time, these improvements just represent the beginning of what’s possible. Looking towards the coming years and decades when humanity will shift life beyond Earth, 3D printing will be a critical technology enabling us to fabricate spare parts and other components in outer space, on the Moon, and on Mars.
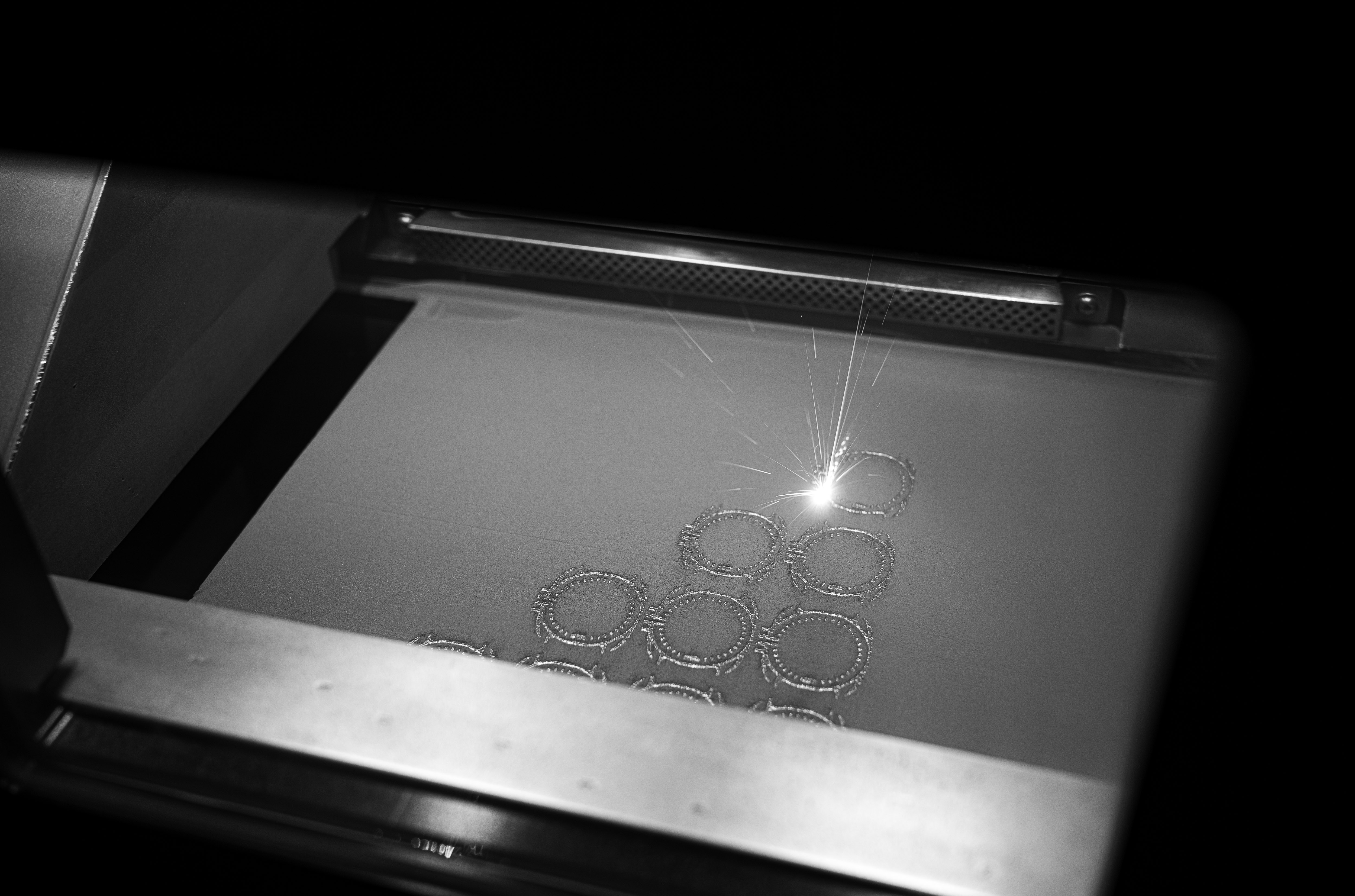
Monolith 3D printed chassis
When designing Monolith, we were able to build on the learnings we had acquired from Project One, especially with regard to 3D printing. The entire team at Barrelhand has also applied years of experience in building and leading companies in the space of digital fabrication. This knowledge has gone towards the creation of new standards in the design and manufacturing of Monolith.
The current iteration of the chassis is monolithically 3D printed in aerospace-grade Ti 6Al-4V titanium, which is one of the multiple aerospace-grade materials that we are exploring. By incorporating skeletonized lugs and internal lattice structures, we were able to reduce the overall weight by over 40% while preserving its full structural integrity. We designed and optimized the chassis with 3D printing in mind, resulting in a geometry with various hollowed-out areas and supporting lattice structures that could not have been realized using any other method of fabrication.
"Designing something which can be monolithically 3D printed without the constraints of traditional manufacturing is the holy grail of engineering. It allows us to create just about any complex geometry, fully optimized towards the harsh conditions of space. I loved flowing through the design process and watching the case form almost organically out of the technical requirements into something that feels like art as a function of engineering."
Karel Bachand, Founder and Chief Engineer, Barrelhand
The Monolith chassis is the result of a collaboration with Materialise, a leading 3D printing solution provider with vast experience working for the aerospace industry. Materialise has established their Competence Center for Metal 3D Printing in Bremen, Germany where they have dedicated engineers with years of experience, offering the full range of AM expertise from design to dedicated parameter setting and final finishing. Far more than just printing a watch case, Materialise and Barrelhand are creating new standards for the design, production, and quality assurance of 3D printed parts for series production applications while meeting ISO standards.
The technology used for 3D printing the chassis is called direct metal laser sintering (DMLS) and works by fusing together thin layers of finely grained metal powder (each grain is a mere 25-50 micrometers, about 4x thinner than a human hair). DMLS is the same technique used by SpaceX to 3D print components of rocket engines. This process removes many limitations of conventional fabrication methods and has enabled us to create a structure that is most ideally suited for the challenges of space — both in terms of weight and strength requirements.
While additive manufacturing offers unprecedented design freedom, it doesn’t mean that it’s easy to work with. During development, we had to understand how the unique forces and temperatures of the build process affect the design to ensure a consistent and high-quality end result. While 3D printing enabled us to create a chassis with complex structures and internal cavities, the design is also self-supporting during the printing process (ie. there are no overhangs greater than 45 degrees). This resulted in organic shapes that are easy to print and flow with the design.
"Design freedom in additive manufacturing enabled us to perfectly combine innovation and lightweight in order to match the visionary approach of the project. With our in-depth knowledge from design to print and finishing, we managed to perfectly consult Barrelhand on developing a professional product for space, ready for serial production.”
Philip Buchholz, Innovation Manager Metal 3D Printing, Materialise
We are currently at the 14th iteration of the chassis which demonstrates another benefit of additive manufacturing: the ability to rapidly iterate on designs. This development journey involved removing material where we could while maintaining a strong, rigid frame, until we reached the current production-ready chassis. The final design strikes a balance between maximizing the potential of scalable additive manufacturing, meeting the requirements of space, and providing gentle surfaces that feel right.
At a mere 10g (equivalent weight of 10 paper clips) for the entire titanium chassis, it will enable Monolith to be in a new category of ultra lightweight watches, true to our mission of building products for the next chapter of space exploration. In the following months, we’ll share more exclusive insights into the development of key features of Monolith. Don’t want to miss any of the updates? Sign up to our newsletter now.
